How do standards help automate label printing?
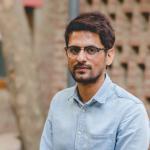
Akash Choudhary, Product Manager at callas software GmbH considers himself as a lifelong student of PDF products and technologies. With a bachelor’s degree in Computer Science and Engineering and a Master of Business Administration (International Management), Akash has gathered experience in small and big firms in software performance testing, marketing, … Read more
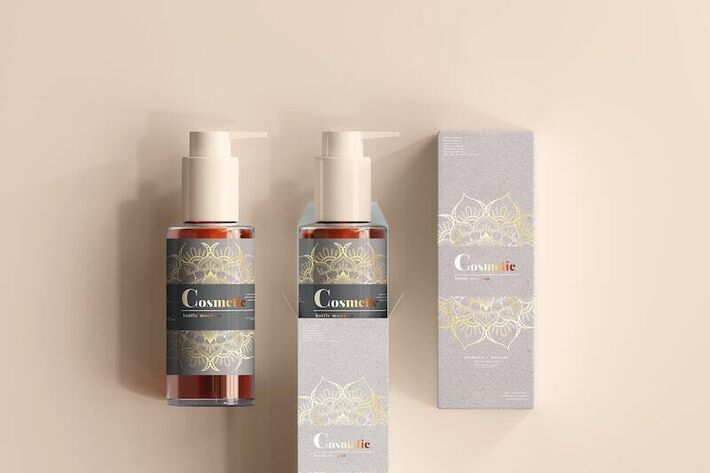
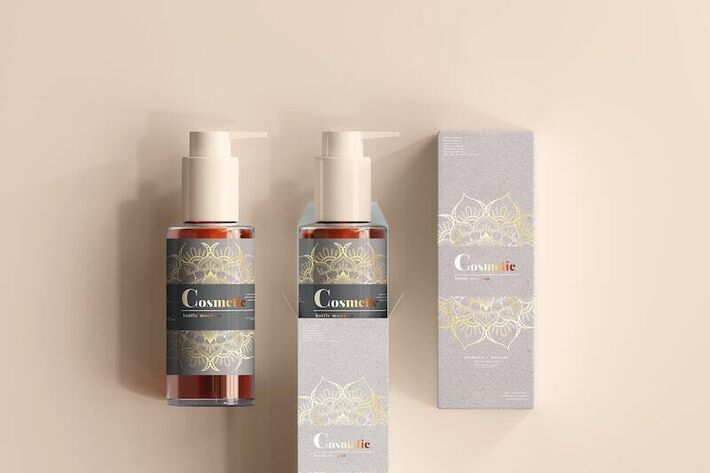
Standardisation ensures uniformity to certain practices in every industry. In printing, standards relieve the print shops of the need to think through all the dependencies, ensure that different solutions work together smoothly, and allow the use of tools that in turn support these standards. These tools can be used to automatically convert PDF files into print-ready files on the basis of profiles. In addition to PDF or PDF/X, the specifications of the Ghent Workgroup are an important standard, particularly for label printing, and have recently become available as GWG 2022.
If you employ GWG profiles, you might know that these profiles allow PDF files to be checked more intelligently. How is that? The applications can now ignore objects that will not cause problems in production, which is the case for fully covered objects, for example. This reduces the number of false positives and, above all, ensures uninterrupted, smooth production.
I think that the Processing Steps standard (ISO 19593) should be mentioned in this context. It was originally developed by the Ghent Workgroup with the aim of storing information about printing and finishing processes - such as cutting, embossing and coating - in a standardized form in a PDF document. To this end, page objects are grouped into layers and standardized metadata is added to these layers, thereby assigning them to a specific processing step.
Especially in label printing, where the objects actually printed are typically not rectangular but have all kinds of shapes (the beer label below for example), these processing steps are a good basis for automating processes.
Print templates in label printing - in addition to the print data itself - usually contain further information that is required during processing. This includes a die-cut contour, a legend or dimensions, which must be recognized as such and taken into account accordingly during checks and corrections. For example, it is necessary to convert all spot colors to CMYK before output on the digital press. Since the dieine is usually also created as a spot color, it must be recognized as such and then excluded from the conversion. The spot color used for the die-cut contour, however, can be named "die-cut", "cutting edge", "die-cutting contour" or similar or completely different, which poses a problem in automated recognition. In addition to their actual function, cutting contours have another meaning for automatic processing, because they define the area for the trimmed final format and thus the relevant page objects. The contour must be located in Processing Steps on a layer in the PDF file. The spot color and also the layer may have arbitrary names, as described, but the layer must contain metadata, which in turn is standardized. If a PDF file has these characteristics, then the PDF engine can reliably recognize the dieline and processes it automatically.
In this context, the question arises as to how all incoming PDF files can be provided with the metadata defined in Processing Steps. Ideally, this is already done when the artwork is created. However, this is supplied by the customer and print shops cannot usually specify that the customer should store the appropriate metadata in their PDF files. An immediately available solution is therefore to make a rule-based, customizable assignment at a central point in the print shop. For example, the spot color can be recognized as a cut contour using intelligent functions and subsequently added as standardized metadata. In the PDF engine, these are then stored in a profile and thus everything that is represented in this spot color is integrated into a layer with the corresponding metadata. The advantage of this customization in the workflow is that the rules used for recognition are applied in a single place. For example, if a new customer from England uses the term "die line", then this can easily be adjusted without having to change the subsequent steps.
If label printers prepare their workflows in the way described, they will be ready for the future and will be able to apply them to standard-compliant print documents without having to make any changes. They can integrate existing PDF engines into their processes and avoid developing their own solutions. This achieves a high level of automation in the production process, which has a positive impact on cost-effectiveness.
callas software finds simple ways to handle complex PDF challenges. As a technology innovator, callas software develops and markets PDF technology for publishing, print production, document exchange and document archiving. callas software helps agencies, publishing companies and printers to meet the challenges they face by providing software to preflight, correct…
Read more